agroindustry
We know how
to solve
IMA is a Business Consulting Firm specialized in generating operational, economic and cultural benefits.
Our experience with Important National and International Companies has allowed us to offer solutions and services according to the different types of industry, guaranteeing results with a proven methodology.
IMA Processes have proven to be a highly profitable investment.
This is our
experience
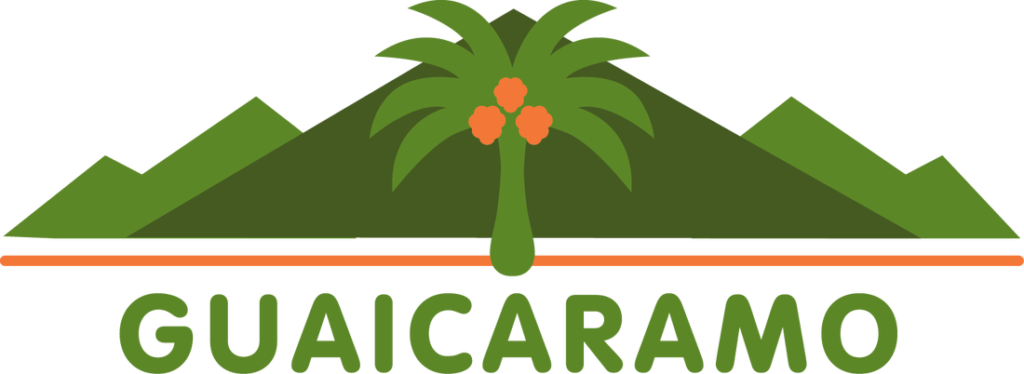
GUAICARAMO
- The project aimed to optimize Transport Logistics and Fruit Harvesting, Health, Pollination, Fertilization, Machinery Workshop, Processing Plant, and Procurement processes to improve the current results.
Some of the benefits obtained during this process are:
- Productivity increases in fruit transport by 62.8%
- Decrease in fuel consumption per kilogram transported by 11.9%
- Decrease in overtime in transport logistics and fruit collection by 52.5%
- Increase in billing due to a better degree of acidity and impurities of 22.2%
- Decrease in the cost of overtime in harvest supervision per kilogram harvested by 19.3%
- Decreased deviation due to excess application in fertilizers of 51.1%
- Decrease in overtime plant health by 19.9%
- 13.3% decrease in fuel consumption per hour in agricultural machinery
- Decrease in the cost of filters and lubricants in agricultural machinery by 7.7%
- Decrease in overtime in the Machinery Workshop by 88.6%
- Increase in the productivity of the Processing Plant by 31.7%
- Increase in kilograms processed due to better filling of wagons by 5.6%
- Decrease in the cost of overtime per kilogram processed in the Processing Plant by 68.0%
- Decrease in the inventory of supplies and raw materials with infinite coverage at 40.8% and with a high coverage range at 29.5%
ROI = 970%
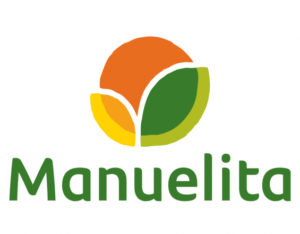
MANUELITA
Design of a Global Factory Indicator and an Incentive Model for Factory personnel.
Factory processes:
- Analysis of current costs and expenses of the operation of the existing organizational structure.
- Statistical analysis of current management results.
- Review current operating costs and expenses of the organizational structure.
- Conceptualize the Global Factory Indicator and validate it.
- Make simulations with actual data from the Global Factory Indicator.
- We defined the expectations to achieve in the Indicator.
- Define the requirements for the work system and the information system necessary for calculating the Global Factory indicator practically.
- Train those responsible for calculating, reading, and analyzing the Global Indicators of the Factory.
Factory Compensation Model:
- Identification of opportunities in the current remuneration and incentive scheme
- Define the objectives expected from the management of each process, which have an integral impact on the factory’s operations and the company’s financial results.
- Carry out an analysis of the current costs and expenses of the operation of the existing structure.
- Identification of opportunities in the current remuneration and incentive scheme
- Define three alternative incentive models for compliance with the Global Factory Indicator.
- Simulate the results of the proposed model with different scenarios of results with actual data.
- Define an evaluation matrix that enables objectively selecting the best incentive model.
- Make the requirements for the work system and the information system that allow the calculation of the incentives of the new model to be generated.
- Review, in conjunction with the audit, the reliability of the information for the generation of the indicators and the calculation of the model.
- Review technical data sheets of the indicators used to calculate the incentive model.
- Review with Human Management the implications of the model.

RIOAILA CASTILLA
Object 1:
Carry out strategic planning to define, establish and make operational a Shared Services Center (SSC) that provides services to Riopaila Castilla S.A. and other companies that do not belong to the business group.
Object 2:
Carry out training and training in Analytics Techniques to improve efficiency and reduce costs and expenses for at least five people working in the Financial Planning area of Riopaila Castilla S.A.
- Identification of the services to be provided by the Shared Services Center.
- Definition of the processes that the Shared Services Center must contain to provide the defined services.
- Definition of the Mission and Objectives of the Shared Services Center and the Missions and Objectives of the processes of the Shared Services Center aligned to the mission and main objectives, for the processes were defined missions and objectives: Accounting, Human management, Procurement, Competitive Intelligence, Legal, Finance, Commercial, Security, Computing, Financial planning.
- The qualitative benefits that would be obtained with the implementation of the Shared Services Center were identified, such as:
- Improvement in customer satisfaction.
- Continuous improvement in processes.
- Service metrics.
- Quick solution to problems.
- Cost-effectiveness.
- Price-quality ratio.
- Low costs.
- Cost containment (low variability)
- Improvement in operational efficiency.
- Reduction of process cycles.
- Learning and business growth through the adoption of best practices.
- Promote the vision of a unique and integrated company either.
- Focus on business and customer.
- Improved reliability and consistency of information
- Enables or facilitates the maintenance of standard processes or activities throughout the organization.
- Comparability: the introduction of standards makes it easier to compare companies.